NDRC's new energy-saving policy for the Year of the Tiger! Oil refining, ethylene and PX are the focus
Release time:
2022-02-21
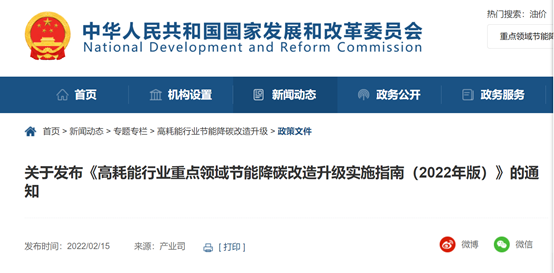
On February 15, 2022, the National Development and Reform Commission released the "Implementation Guidelines for Energy Conservation and Carbon Reduction in Key Areas of High-Energy Consumption Industries (2022 Edition)" on its official website, requiring the use of advanced and applicable technologies and equipment to accelerate the green and low-carbon transformation of the petrochemical industry.
The "Implementation Guidelines" covers 17 key sub-industries, including petrochemicals, chemicals, building materials, steel, and nonferrous metals. It clarifies the basic situation of energy efficiency in each sub-industry and puts forward the work direction and goals for energy-saving and carbon-reduction transformation and upgrading.
The National Development and Reform Commission believes that the petrochemical industry is a basic industry and an important pillar of the national economy, and its level of industrial development is one of the important indicators of a country's industrialization and modernization. my country's petrochemical industry is large in scale, with a long industrial chain, and its energy consumption and carbon emissions are among the highest in all industries. Sub-industries such as oil refining, ethylene, and paraxylene (PX) are key areas for energy conservation and carbon reduction in the petrochemical industry. The Guidelines propose energy-saving and carbon-reduction transformation and upgrading plans for the above three sub-industries, analyze the problems existing in the main processes and energy-consuming links, and propose reference suggestions for specific work directions and technical choices in terms of the development and application of cutting-edge technologies and the popularization and promotion of mature technology equipment and processes, and further quantify the implementation goals of the "14th Five-Year Plan" energy-saving and carbon-reduction transformation.
For the oil refining industry, the "Implementation Guidelines" proposes to strengthen the development and application of deep refining technologies such as residue slurry bed hydrogenation and other processing of inferior heavy oil raw materials, advanced separation and molecular refining, low-cost increased production of olefins and aromatics, and direct cracking of crude oil; accelerate the popularization and promotion of advanced control technology, cold regeneration agent circulation catalytic cracking technology, compressor control optimization and regulation technology, high-efficiency air preheaters, high-efficiency heat exchangers, and distillation system optimization technology.
For the ethylene industry, the "Implementation Guidelines" propose to promote the development and application of direct crude oil cracking technology, electric cracking furnace technology, equipment electrification and green energy coupling utilization technology; require to accelerate the popularization and promotion of online coking technology for cracking furnaces, advanced viscosity reduction tower viscosity reduction technology, twisted sheet tubes and other cracking furnace tubes and new forced ventilation burners, waste heat utilization heat pump integrated technology, advanced optimization control technology, and furnace tube enhanced heat transfer technology.
Regarding the key sub-industries of energy and chemical industry involved in the new energy conservation policy of the National Development and Reform Commission, ASIACHEM Consulting has extracted the key contents as follows.
1. Oil refining industry
According to the "Energy Efficiency Benchmark and Baseline Levels in Key Areas of High-Energy Consumption Industries (2021 Edition)", the benchmark level for oil refining energy efficiency is 7.5 kg of standard oil/(ton·energy factor) and the base level is 8.5 kg of standard oil/(ton·energy factor). As of the end of 2020, about 25% of my country's oil refining industry had energy efficiency better than the benchmark level, and about 20% had energy efficiency lower than the benchmark level.
Strictly implement policy constraints and eliminate backward and inefficient production capacity. Strictly implement relevant laws and regulations on energy conservation, environmental protection, quality, safety technology, and policies such as the "Guidelines for Industrial Structure Adjustment", and eliminate 2 million tons/year and below atmospheric and vacuum distillation units, kettle distillation units that use open flame high-temperature heating to produce oil products, etc. in accordance with laws and regulations. For refining capacity with energy efficiency levels below the benchmark value and that cannot be upgraded to above the benchmark value, accelerate the withdrawal in accordance with the requirements of equal or reduced replacement by promoting the superior and eliminating the inferior, and promoting the large and suppressing the small.
Target of oil refining industry: by 2025, the proportion of production capacity above the benchmark level of energy efficiency in the oil refining industry will reach 30%, the production capacity below the benchmark level of energy efficiency will be accelerated to withdraw, the industry will have a significant effect on energy conservation and carbon reduction, and the green and low-carbon development capacity will be greatly improved.
2. Ethylene industry
According to the "Energy Efficiency Benchmark and Baseline Levels in Key Areas of High-Energy Consumption Industries (2021 Edition)", the benchmark level for ethylene energy efficiency is 590 kg of standard oil per ton and the base level is 640 kg of standard oil per ton. By the end of 2020, about 20% of my country's steam cracking ethylene production capacity had energy efficiency better than the benchmark level, and about 30% of the total capacity had energy efficiency lower than the benchmark level.
The policy requires the promotion of the development and application of crude oil direct cracking technology and electric cracking furnace technology, and the strengthening of the application of equipment electrification and green energy coupling utilization technology.
Energy system optimization. Use advanced optimization control technology to promote the optimization of the heat exchange network of the device and improve the overall heat exchange efficiency of the device. Use the intermediate reflux technology of the quenching oil tower to recover the intermediate heat of the quenching oil tower. Use the furnace tube enhanced heat transfer technology to improve thermal efficiency. Add an air preheater to use the waste heat of ethylene and other devices to preheat the combustion air, reduce fuel consumption, and reasonably recover the heat of heat sources such as flue gas, quenching water, and steam condensate. Use low-temperature ethane, propane, and liquefied natural gas (LNG) cold energy utilization technology to reduce the energy consumption of the device.
Optimize and adjust raw materials. Use low-carbon, light, and high-quality cracking raw materials to increase the yield of ethylene products and reduce energy consumption and carbon emission intensity. Promote the intensive concentration and optimal utilization of regional high-quality cracking raw material resources to improve resource utilization efficiency.
Strictly implement policy constraints and eliminate backward and inefficient production capacity. Strictly implement relevant laws and regulations on energy conservation, environmental protection, quality, safety technology, and policies such as the "Guidelines for Industrial Structure Adjustment" to accelerate the elimination of ethylene units below 300,000 tons/year. For ethylene units with energy efficiency levels below the benchmark value and unable to reach above the benchmark value through energy-saving transformation, accelerate the elimination and withdrawal.
Work objectives of ethylene industry: by 2025, the scale level of ethylene industry will be greatly improved, the trend of light weight, low carbonization and high quality of raw material structure will be more obvious, the benchmark production capacity ratio of ethylene industry will reach more than 30%, the production capacity below the benchmark level of energy efficiency will be upgraded in an orderly manner, the energy saving and carbon reduction effect of the industry will be remarkable, and the green and low-carbon development capacity will be greatly improved.
3. Modern coal chemical industry
According to the "Energy Efficiency Benchmarks and Base Levels in Key Areas of High-Energy Consumption Industries (2021 Edition)", the energy efficiency benchmark level of coal-to-methanol using lignite as raw material is 1,550 kg of standard coal per ton, and the base level is 2,000 kg of standard coal per ton; the energy efficiency benchmark level of coal-to-methanol using bituminous coal as raw material is 1,400 kg of standard coal per ton, and the base level is 1,800 kg of standard coal per ton; the energy efficiency benchmark level of coal-to-methanol using anthracite as raw material is 1,250 kg of standard coal per ton, and the base level is 1,600 kg of standard coal per ton. The energy efficiency benchmark level of coal-to-olefins (MTO route) is 2,800 kg of standard coal per ton, and the base level is 3,300 kg of standard coal per ton. The energy efficiency benchmark level of coal-to-ethylene glycol is 1,000 kg of standard coal per ton, and the base level is 1,350 kg of standard coal per ton. As of the end of 2020, about 15% of my country's coal-to-methanol industry had energy efficiency better than the benchmark level, and about 25% had energy efficiency below the benchmark level. About 48% of the coal-to-olefins industry had energy efficiency better than the benchmark level, and all of its capacity was higher than the benchmark level. About 20% of the coal-to-ethylene glycol industry had energy efficiency better than the benchmark level, and about 40% had energy efficiency below the benchmark level.
Work objectives of modern coal chemical industry: by 2025, the production capacity of coal-to-methanol, coal-to-olefin and coal-to-ethylene glycol industries above the benchmark level of energy efficiency will reach 30%, 50% and 30% respectively, and the production capacity below the benchmark level will be basically cleared to zero. the industry will have significant energy saving and carbon reduction effects, and the green and low-carbon development capacity will be greatly improved.
4. Calcium carbide industry
According to the "Energy Efficiency Benchmark and Baseline Levels in Key Areas of High-Energy Consumption Industries (2021 Edition)", the energy efficiency benchmark level of calcium carbide is 805 kg of standard coal per ton and the base level is 940 kg of standard coal per ton. As of the end of 2020, the production capacity of my country's calcium carbide industry with energy efficiency better than the benchmark level accounted for about 25%.
Strictly implement policy constraints and eliminate backward and inefficient production capacity. Strictly implement relevant laws and regulations on energy conservation, environmental protection, quality, safety technology, and policies such as the "Guidelines for Industrial Structure Adjustment", eliminate internal combustion calcium carbide furnaces, and guide the long-term shutdown of ineffective calcium carbide production capacity to voluntarily withdraw. For production equipment with energy efficiency levels below the benchmark value and unable to reach above the benchmark value through energy-saving transformation, accelerate elimination and withdrawal.
Work objectives of the calcium carbide industry: by 2025, the proportion of production capacity above the energy efficiency benchmark level in the calcium carbide field will reach 30%, the production capacity below the energy efficiency benchmark level will be basically cleared, the industry will have a significant effect on energy conservation and carbon reduction, and the green and low-carbon development capacity will be greatly enhanced.
5. Paraxylene industry
According to the "Energy Efficiency Benchmark and Baseline Levels in Key Areas of High-Energy Consumption Industries (2021 Edition)", the energy efficiency benchmark level for paraxylene is 380 kg of standard oil per ton, and the base level is 550 kg of standard oil per ton. As of the end of 2020, about 23% of my country's paraxylene production capacity had energy efficiency better than the benchmark level, and about 18% had energy efficiency lower than the benchmark level.
Strictly implement relevant laws and regulations on energy conservation, environmental protection, quality, safety technology, and policies such as the "Guidelines for Industrial Structure Adjustment", and accelerate the elimination of single-series paraxylene units with a capacity of less than 600,000 tons per year. For paraxylene units whose energy efficiency level is below the benchmark value and cannot be raised above the benchmark value through energy-saving transformation, accelerate the elimination and withdrawal.
Work objectives of the paraxylene industry: by 2025, the scale level of paraxylene industry installations will be significantly improved, the proportion of production capacity above the energy efficiency benchmark level will reach 50%, the production capacity below the energy efficiency benchmark level will be basically cleared, the industry will have a significant effect on energy conservation and carbon reduction, and the green and low-carbon development capacity will be greatly improved.
The article is reproduced from:
https://mp.weixin.qq.com/s/AKvEA5uWgVQ5O0_jf4EgMA
Related pictures and information are from: Petrochemical Forum
A high-tech enterprise that develops catalytic new materials, with a core scientific and technological innovation team from the University of Science and Technology of China
Navigation
Follow us

Copyright©2024 Anhui Huanxuan Material Technology Co., Ltd.